According to the working conditions of the mold, the mold accessories can be divided into the following three categories:
1. Cold work
Die accessories: including cold die, cold heading die, cold extrusion die, drawing die, wire drawing die, rolling die, shearing die, etc.
2. Hot work die: including hot forging die (hot forging die, high-speed hammer forging die, precision forging die), hot extrusion die, hot blanking die, die casting die, etc.
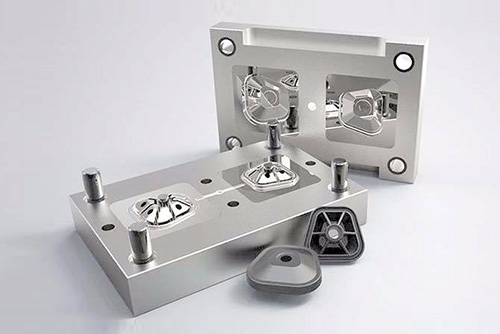
3. Forming mold accessories: including plastic mold, rubber mold, ceramic mold, glass mold, powder metallurgy mold, etc. Within the range of 52HRC, plastic molds are usually considered within 45-60HRC. ☆ Hardness is a kind of performance index to measure the degree of softness and hardness of the material, and refers to the ability of the material to resist local deformation, especially plastic deformation, indentation or scratch. It is a comprehensive reflection of strength, plasticity, toughness, wear resistance and other indicators, so the hardness value is often marked on the part drawing as a technical requirement. ☆ Hot hardness refers to the ability of the mold to maintain high hardness under heat or high temperature conditions; for example, hot work molds and some cold work molds are required to have certain hot hardness. The hardness and hot hardness of the material mainly depend on the composition of the material, the heat treatment process and the surface treatment process. It can reflect the wear resistance level of each steel type; the test is based on Cr12MoV steel (ε = 1.0).
4. Fatigue resistance--Reflects the performance index of the material to resist fatigue damage under the action of alternating load. Hot work dies often work under conditions of rapid cooling and heating, and different degrees of thermal fatigue must occur, and cracks occur. Therefore, it is desirable to have high cold and thermal fatigue resistance to avoid early failure. Titanic sinking reason
(2) Process performance requirements
1. Hot working process performance, including forging, casting, welding and other properties. According to the different manufacturing processes of the mold, different processing performance requirements can be proposed. These performance requirements are affected by factors such as the chemical composition of the mold material, metallurgical quality, and organizational state.
2. Cold processing technology performance including cutting, polishing, grinding, cold extrusion and cold drawing performance. Mold products sometimes require high surface quality, low surface roughness and high precision, so they have higher requirements for cutting performance and polishing performance.
3. Heat treatment process performance In fact, it is a kind of hot processing technology performance. In mold failure accidents, the factors caused by heat treatment account for about 52% of the total failures. The quality of heat treatment process performance has a greater impact on the quality of the mold. It requires small heat treatment deformation, wide quenching temperature range, small overheating sensitivity, low decarburization sensitivity, low quenching cracking tendency, etc. In particular, it requires sufficient hardenability and hardenability. It can be manufactured first, and it becomes more prominent for ease of manufacturing when the batch is large.
(3) Supply can be ensured. The selected materials should take into account my country's resources and actual supply situation, use imported materials as little as possible, and the varieties and specifications should be as few and concentrated as possible to facilitate procurement management. (4) Reasonable economy. The selected materials are required to have a simple production process, high yield, and low cost. In order to meet the requirements of performance and longevity, choose materials with low prices as much as possible to reduce costs. 7. Specific considerations for mold material selection In the actual design and manufacture of molds, the specific selection of materials should be comprehensively analyzed to consider the following factors.
(4) Factors of working conditions of the mold
1. The size and speed of the bearing force
(Impact condition) High stress requires high strength of the material; high impact requires good toughness.
2. Working temperature The three types of molds for cold work, plastic and hot work are very different, so the heat resistance requirements of the materials are very different.
3. The quality of the product requires high precision and low surface roughness. The materials selected must be made from the composition and material to ensure good cutting and polishing performance when the mold is manufactured. Stability or high accuracy and low surface roughness value.
4. Material of the product Whether the processed product is metallic or non-metallic material, the deformation resistance and working temperature of the different raw materials are very different, the working conditions of the mold are very different, and the selected mold material is very different. same. The mold composition can be divided into working parts and auxiliary parts. The former is in direct contact with the processed material, which requires higher material performance than the latter. For example, the working part (profile or blade) of the convex and concave molds requires high hardness, wear resistance, and heat resistance; non-working parts can be appropriately reduced, but certain strength and toughness must be guaranteed. For the auxiliary parts of the mold, including fasteners, guide parts, etc., materials can be selected according to their performance requirements. (V) Factors of the manufacturing process of the mold The different processing methods and processes of cold processing (cutting, polishing, grinding) and hot processing (forging, casting, welding) used in manufacturing should be considered, and appropriate materials should be selected to suit them. The selection of materials for the manufacturing of molds by different methods of manual and mechanical should be different. The cost of manual molds is high, and better materials should be selected as much as possible. Section 2 Cold Work Die Material and Its Heat Treatment Cold work die is a die used for pressure processing or other processing of materials at room temperature. It is mainly divided into punching die, drawing and forming die, cold heading die and cold extrusion mold. 1. Characteristics of various types of cold work dies (1) Punching die It obtains workpieces with certain shapes and sizes with cutting edges, punching and separating materials (mainly plates) during work