In the processing of precision plastic mold parts, we often see plastic products lacking material, resulting in stress cracks, smears, dents, silver streaks, deformation, cracks, mesh cracks, whitening, weld marks and other issues. And these problems will affect the quality of precision plastic mold parts processing. So, how do we solve these problems in the processing of precision plastic mold parts?
1. Increase the temperature of the plastic mold, increase the temperature of the barrel, and increase the injection pressure. Add a gas escape groove (depth 0.02~0.04mm) width 5~10mm on the parting surface. Increase the gate and increase the flow edge. In the case of a large number of molds, the cavity lacks the material to expand the gate of the cavity, and the configuration of the flow edge is changed, and the gas escape pin is added to improve the plastic. The finish of the mold.
2. Increase the injection pressure, extend the injection pressure holding time, reduce the temperature of the barrel and the temperature of the plastic mold, and force the cooling in the place where the dent is generated. Fill the flow edge where the dent is created. When there is a narrow place on the side of the material where the dent is generated, the side is thick. The difference in thickness of the design article should be completely avoided. Ribs that are prone to dents should be as short as possible.
3. Avoid the difference in thickness of the designed product, and attach the gate to the place where the thickness of the product is thick. Fully cool and solidify in the plastic mold (extend the cooling time chronograph), increase the barrel temperature, reduce the injection pressure, and make the plastic mold cool evenly.
4, to avoid the difference in thickness of the product, set the gate in the place where the thickness of the product is large, because the straight line is easy to cause warpage, make a large R curve, the plastic mold can reversibly bend the product, increase the number of the ejector rod, increase the stripping angle degree.
5, to avoid the difference in the thickness of the design of the product, add a gate in the thick thickness of the product, to understand the use of the product, if appropriate, use materials with good fluidity. The material is completely dry. It is not good to use high temperature and short time drying. Generally, it is dried at 85 °C for 4 hours to increase the temperature of the plastic mold, reduce the temperature of the heating cylinder, and keep the barrel of the barrel warm to make the flow side thicker.
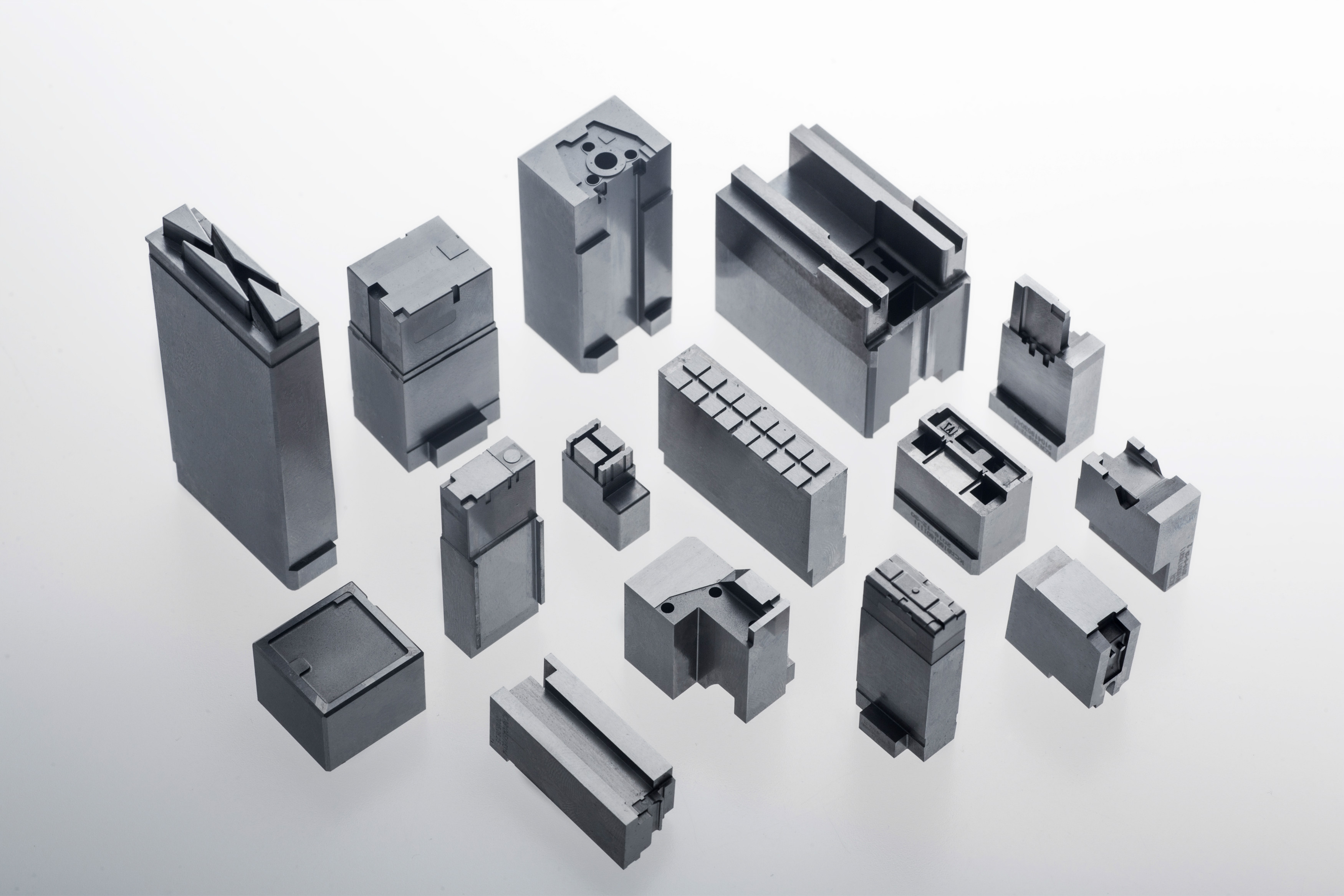